Accuracy is the foundation of any construction project. A small mistake can lead to structural issues, project delays, and cost overruns. Studies indicate that construction rework accounts for nearly 30% of total project costs, often due to inaccurate measurements and outdated documentation.
That’s why modern AEC professionals are turning to 3D laser scanning services—a game-changing technology that brings unparalleled precision and efficiency to the construction process.
Using high-definition surveying (HDS) and LiDAR technology, laser scanners capture as-built measurements with millimeter accuracy, creating a digital twin of the construction site.
This data is then converted into a 3D BIM model, a real-time reality capture of existing conditions. The result? 80% fewer errors in construction documentation, seamless BIM integration, and reduced risk at every stage of the project.
With proven applications in site analysis, project efficiency, and cost savings, 3D laser scanning for construction is no longer an option—it’s becoming the new standard.
In fact, a recent survey by Dodge Data & Analytics found that 74% of construction professionals believe laser scanning improves project coordination and reduces rework costs.
But how does it work, and why should you use it for your next infrastructure project? Let’s dive in.
What Is 3D Laser Scanning for Construction Projects?
3D laser scanning for construction is a surveying technology that uses laser beams to capture highly detailed and precise digital representations of a construction site, structure, or object.
This process generates a point cloud—a collection of millions of data points that accurately depict real-world conditions. The scan data is then converted into a 3D model for use in BIM integration, design validation, and construction accuracy.
How Does 3D Laser Scanning Work?
The process of 3D laser scanning for construction involves capturing highly accurate as-built measurements and transforming them into usable 3D data for project planning, design validation, and quality control. Here’s how it works:
1. Scanning the Construction Site
A laser scanner is placed at multiple locations around the construction site to collect high-definition spatial data. These scanners emit millions of laser pulses per second, bouncing off surfaces and returning to the scanner. Each returning pulse is recorded as a point in space, creating a raw dataset known as a point cloud.
- Fixed LiDAR scanners are mounted on tripods for static scans of buildings or infrastructure.
- Mobile LiDAR scanners are attached to drones or vehicles for large-scale terrain and infrastructure projects.
- Handheld scanners are used for detailed scans of interior spaces or tight areas.
This step reduces surveying time by up to 75% compared to traditional methods, so you can get data faster.
2. Generating the Point Cloud
As laser pulses hit different surfaces, the scanner collects millions of data points, which are assembled into a point cloud—a precise 3D representation of the scanned environment. This raw scan data contains critical information, such as dimensions, spatial relationships, and surface textures.
Why is the point cloud important?
- It provides accurate measurement of existing conditions, eliminating errors that contribute to 52% of rework in construction projects.
- It ensures construction accuracy by identifying discrepancies between plans and reality.
- It enhances BIM integration by forming a data-rich foundation for digital models.
3. Processing and Aligning Scan Data
Once the point cloud is captured, it is processed using specialized surveying technology and software such as Autodesk ReCap, Leica Cyclone, or Bentley Pointools. The software stitches together multiple scans from different locations, aligning them into a single cohesive 3D dataset.
- Noise reduction is applied to remove irrelevant data points.
- Point cloud registration ensures all scans align correctly.
- Georeferencing integrates scan data with real-world coordinates for precision.
4. Converting the Point Cloud to a 3D BIM Model
The processed point cloud is imported into BIM software like Autodesk Revit or Navisworks. From here, it is converted into a 3D BIM model, where different building components (walls, floors, MEP systems, etc.) are reconstructed digitally.
Why is BIM integration crucial?
- Enables clash detection before construction begins.
- Helps track construction progress with updated scans.
- Reduces errors, ensuring project efficiency and cost reduction.
5. Data Utilization for Construction Accuracy
Once the 3D model is created, it becomes a powerful tool for ensuring construction accuracy and improving overall project management. The scan data allows teams to compare the as-built environment with the design model, ensuring that everything aligns correctly.
It also helps track the construction process, reducing costly errors and delays. By integrating 3D laser scanning services with BIM workflows, AEC professionals can make informed decisions based on real-time data.
Here’s how the data is utilized:
- Reality Capture: Provides a highly detailed digital twin of the site, ensuring precise documentation.
- Construction Process Optimization: Aligns workflows with actual site conditions, minimizing delays.
- Risk Mitigation: Detects clashes and discrepancies before construction begins, preventing rework.
- As-Built Documentation: Maintains a comprehensive digital record for future modifications or renovations.
Best Software for 3D Laser Scanning and BIM Integration
Now that we understand the importance of 3D laser scanning for construction, let’s talk about the best software solutions that can process and integrate point cloud data seamlessly.
Choosing the right software is crucial because raw scan data is huge, complex, and unstructured—without the right tools, it’s nearly impossible to convert it into usable BIM models.
Here are the top three software programs that dominate the scan-to-BIM industry:
1. Autodesk ReCap Pro—Best for BIM Integration
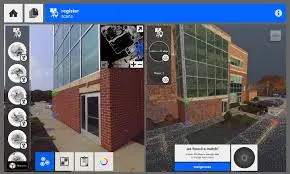
Autodesk ReCap Pro is widely regarded as the best software for processing laser scans and integrating them directly into BIM platforms like Revit and Navisworks. It allows professionals to clean, register, and convert point cloud data into precise 3D models.
Key Features:
- Seamless integration with Autodesk BIM tools (Revit, Navisworks, AutoCAD)
- Fast point cloud registration and cleanup
- RealView immersive visualization for interactive site analysis
- Smart AI-based noise filtering to improve scan accuracy
Why is it important?
BIM professionals working on renovation, heritage preservation, or as-built documentation often prefer ReCap Pro because it allows direct integration of laser scans into Revit models, reducing manual work.
2. Leica Cyclone—Best for High-Precision Scan Processing
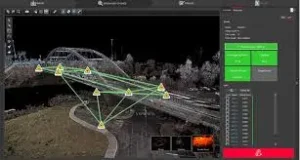
Leica Cyclone is an industry-standard software for professionals who need high-precision scan processing for large-scale infrastructure, industrial plants, and geospatial projects.
Key Features:
- Advanced georeferencing for accurate positioning of scan data
- Automated feature extraction (walls, pipes, MEP elements)
- Support for billion-point datasets without performance lag
- Powerful clash detection tools for identifying construction errors
Why is it important?
Large-scale projects like railways, highways, and complex industrial sites require laser scans to be aligned with extreme accuracy. Leica Cyclone ensures sub-millimeter precision, making it the go-to choice for surveyors and engineers.
3. FARO Scene—Best for Real-Time Visualization
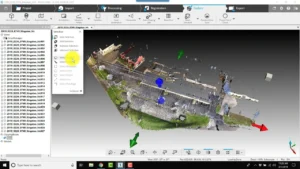
FARO Scene stands out for its fast, real-time point cloud processing and visualization, making it a favorite for heritage conservation, forensic analysis, and facility management.
Key Features:
- Automatic scan alignment for quick data processing
- Mesh and surface modeling for creating digital twins
- Augmented Reality (AR) visualization for project insights
- Web-based collaboration for remote teams
Why is it important?
For projects requiring quick site documentation and visualization, such as restoration of historical buildings or forensic site analysis, FARO Scene allows teams to interact with 3D laser scan data in real time.
Benefits of 3D Laser Scanning for Construction
The adoption of 3D laser scanning services in construction has transformed the industry, offering unmatched precision and efficiency. By integrating this technology, construction professionals can reduce errors, save time, and improve overall project execution. Let’s explore the key benefits:
1. Unmatched Accuracy and Precise Measurements
Traditional surveying methods leave room for human error, but 3D laser scanning for construction eliminates this risk by capturing millimeter-accurate measurements. The resulting point cloud data provides a detailed representation of the existing site, ensuring precise planning and execution.
2. Faster Data Collection and Project Efficiency
Time is money in construction, and laser scanning technology dramatically speeds up site analysis. What once took days with manual surveying can now be done in minutes or hours, streamlining the entire construction process and improving productivity.
3. Cost Reduction and Waste Minimization
Errors in construction lead to costly rework and material waste. With 3D laser scanning, teams can identify discrepancies early, reducing unexpected expenses and ensuring resources are used efficiently. This results in better cost control and improved project profitability.
4. Risk Mitigation and Safety Improvement
Construction sites come with inherent risks. High-definition surveying (HDS) and LiDAR technology allow for remote site analysis, reducing the need for workers to physically enter hazardous zones. This enhances on-site safety and minimizes potential accidents.
5. Enhanced BIM Integration and Digital Twin Creation
The integration of laser scanning services with BIM workflows enables the creation of a digital twin—a highly accurate 3D BIM model of the site. This not only aids in design validation but also helps with future renovations and facility management.
Challenges of 3D Laser Scanning for Construction
While 3D laser scanning for construction is revolutionizing the construction industry, its implementation is not without hurdles. From high costs to technical complexities, several challenges must be addressed before fully integrating this technology into everyday workflows.
1. High Initial Investment Costs
Adopting laser scanning technology requires a significant upfront investment in hardware, software, and skilled personnel. Advanced LiDAR scanners and high-definition surveying (HDS) tools can be expensive, making it difficult for small to mid-sized firms to justify the cost.
2. Complexity in Data Processing and Management
Laser scanning generates massive point cloud datasets, which require powerful computing resources to process efficiently.
- File sizes are enormous, demanding high storage capacity and fast processing speeds.
- Converting scan data into a 3D BIM model is time-consuming and requires skilled professionals.
- Integrating scanned data with existing BIM workflows may require additional software or plugins.
3. Skill Gap and Training Requirements
Many construction professionals lack the expertise to fully utilize laser scanning technology. Surveyors, architects, and engineers must be trained in data acquisition, processing, and interpretation to ensure accurate results. The learning curve can slow adoption in firms unfamiliar with reality capture techniques.
4. Environmental and Site Limitations
Several on-site conditions can impact the accuracy of laser scanning:
- Highly reflective materials like glass or polished metal can distort scan results.
- Weather conditions such as heavy rain, fog, or direct sunlight may affect laser accuracy.
- Cluttered job sites or moving objects can obstruct scans, requiring multiple passes to capture complete data.
5. Compatibility and Integration Issues
Not all construction software platforms seamlessly support laser scan data. Different file formats—such as IFC, Revit, and point clouds—may require conversion before they can be used effectively.
Ensuring compatibility between laser scanning outputs and BIM software can add extra steps to the workflow.
The Future of 3D Laser Scanning for Construction
The future of 3D laser scanning for construction is set to revolutionize the industry even further, bringing greater efficiency, precision, and cost savings to complex projects.
As technology advances, new developments in laser scanning, reality capture, and digital twin integration will reshape how we approach construction workflows.
1. Enhanced Accuracy with AI and Machine Learning
The combination of 3D laser scanning and artificial intelligence (AI) will lead to automated analysis of point cloud data, reducing errors and speeding up project timelines.
AI-driven data processing will improve clash detection, quality control, and predictive maintenance, making construction sites more efficient.
2. Integration with Digital Twins for Real-Time Monitoring
As digital twin technology becomes mainstream, laser scanning will play a crucial role in maintaining as-built models that continuously update in real time.
This will enable construction teams to monitor project progress, compare as-designed vs. as-built conditions, and optimize facility management.
3. Cloud-Based Collaboration and Remote Access
With cloud-based platforms, 3D laser scan data will be accessible from anywhere, allowing stakeholders to collaborate seamlessly. This will streamline the BIM integration process, improve project coordination, and reduce costly miscommunications.
4. More Affordable and Portable Laser Scanners
As technology advances, laser scanners will become smaller, more affordable, and more user-friendly. Handheld LiDAR devices and mobile scanning solutions will allow construction teams to capture accurate measurements on-site quickly, making surveying technology more accessible to all projects.
5. Sustainability and Reduced Material Waste
By improving accuracy in as-built measurements and site analysis, 3D laser scanning for construction will contribute to sustainable development. Fewer errors mean less material waste, lower costs, and a reduced environmental footprint for infrastructure projects.
Conclusion:
3D laser scanning for construction is revolutionizing the industry by providing unmatched accuracy, efficiency, and cost savings. With its ability to capture millions of data points in minutes, this technology eliminates manual errors, enhances BIM integration, and ensures that projects stay on schedule and within budget.
From site analysis and as-built documentation to risk mitigation and construction progress tracking, 3D laser scanning offers a comprehensive solution for modern construction challenges.
McKinsey & Company reports that construction technology adoption, including laser scanning, can improve project efficiency by up to 50% and reduce overall costs by 10-20%.
While initial investment and technical expertise are required, the long-term benefits—such as reduced rework, improved collaboration, and streamlined project execution—make it an indispensable tool for AEC professionals.
As the construction industry moves towards greater digitalization, 3D laser scanning, LiDAR, and reality capture will become the backbone of precision and efficiency in project execution.
A 2024 report by MarketsandMarkets estimates that the 3D scanning market will grow to $6.9 billion by 2028, highlighting its increasing adoption.
Adopting this technology today means staying ahead of the curve, reducing risks, and delivering flawless construction projects.